一、D階段
1、項(xiàng)目的選定
高爐礦渣超細(xì)粉項(xiàng)目是公司節(jié)能減排、資源循環(huán)的主要項(xiàng)目之一,位于發(fā)電廠燃化作業(yè)區(qū)與煉鐵廠干煤棚之間。它可將高爐礦渣進(jìn)行深加工,產(chǎn)出高附加值超細(xì)粉,應(yīng)用于水泥和混凝土行業(yè),可有效提高高爐尾渣利用價(jià)值。此項(xiàng)目將產(chǎn)生的高爐水渣全部利用,從而實(shí)現(xiàn)高爐礦渣由原來的外排銷售到資源的產(chǎn)品化深加工發(fā)展利用,以此為公司創(chuàng)造更大的高附加值。
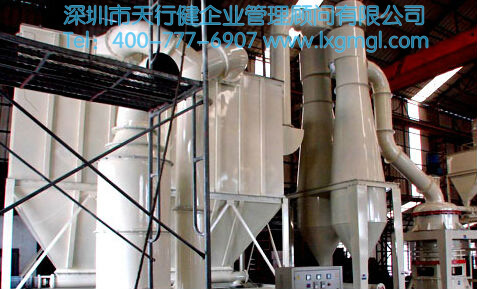
2、問題的陳述
統(tǒng)計(jì)數(shù)據(jù)表明2014年6月一2015年1月,超細(xì)粉的月平均自動(dòng)控制系統(tǒng)故障時(shí)間為467 min,且波動(dòng)較大,最長(zhǎng)故障時(shí)間為1100 min,最短故障時(shí)間為210 min。如果以故障時(shí)間不超過287 min為標(biāo)準(zhǔn),則大約有75%的時(shí)間超過了這個(gè)標(biāo)準(zhǔn)。
3、Y的定義及分解
Y為自動(dòng)控制系統(tǒng)故障時(shí)間(計(jì)算機(jī)控制系統(tǒng)故障時(shí)間與儀表控制系統(tǒng)故障時(shí)間之和)。Y分解為兩部分,即計(jì)算機(jī)控制系統(tǒng)故障時(shí)間與儀表控制系統(tǒng)故障時(shí)間。缺陷是自動(dòng)控制系統(tǒng)故障時(shí)間大于287 min。
4、項(xiàng)目基線及目標(biāo)的設(shè)定
項(xiàng)目的基線為467 min/月,為完成公司下達(dá)的年生產(chǎn)任務(wù),目標(biāo)定為287 min/月,提高70%,符合黑帶項(xiàng)目(公司特制定“高爐礦渣超細(xì)粉項(xiàng)目”為置帶項(xiàng)目)目標(biāo)70%-90%的提高原則。
二、M階段
M階段的目的是找到導(dǎo)致此問題的原因有哪些,并找出關(guān)鍵因子是什么。工作重點(diǎn)是在D階段工作的基礎(chǔ)上,進(jìn)一步明確Y的測(cè)量,并通過收集X(影響因子)和Y的測(cè)量數(shù)據(jù),定量化地描述Y。特別是通過過程分析,認(rèn)識(shí)Y的波動(dòng)規(guī)律,揭示過程改進(jìn)的機(jī)會(huì),識(shí)別實(shí)現(xiàn)項(xiàng)目目標(biāo)的可能途徑和改進(jìn)方向。
1、Y的測(cè)量系統(tǒng)分析
根據(jù)2014年6月一2015年1月份所有故障測(cè)試的時(shí)間共14次,與數(shù)據(jù)庫記錄時(shí)間一致的為13次,不一致的為1次。按這組數(shù)據(jù)計(jì)算一致性比率:
一致性比率=一致次數(shù)/測(cè)試總次數(shù)=13/14=92.9%
由計(jì)算可以看出,一致性比率為92.9%,大于90%。說明本測(cè)量系統(tǒng)良好,可以信賴。
2、Y的流程能力分析
①對(duì)2014年6月-2015年1月的故障時(shí)間進(jìn)行受控驗(yàn)證,用Minitab軟件繪制單值一移動(dòng)極差控制圖,經(jīng)檢驗(yàn),發(fā)現(xiàn)這些數(shù)據(jù)都只受隨機(jī)因素影響,因此這個(gè)過程是受控的。故障時(shí)間I-MR(單值一移動(dòng)極差)控制圖如圖1所示。
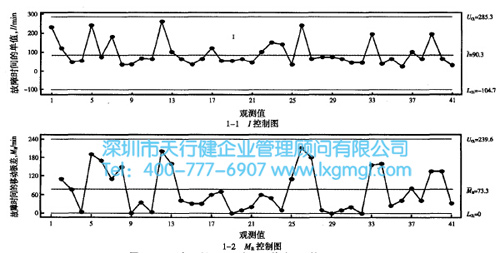
圖1
②對(duì)2014年6月一2015年1月的故障時(shí)間進(jìn)行正態(tài)性檢驗(yàn),P值=0.099>0.05,符合正態(tài)性。正態(tài)性檢驗(yàn)圖如圖2所示。
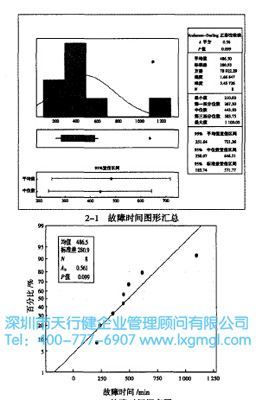
圖2
③對(duì)2014年6月一2015年1月的故障時(shí)間進(jìn)行過程能力分析,過程能力指數(shù)CPK=0.64,過程能力較差,急需對(duì)過程進(jìn)行全面改進(jìn)。
3、查找因子
通過故障時(shí)間長(zhǎng)魚骨圖對(duì)影響故障時(shí)間的因子進(jìn)行查找。
4、因子篩選
通過對(duì)42個(gè)與故障時(shí)間長(zhǎng)有關(guān)的因子進(jìn)行矩陣分析,從中篩選出了23個(gè)分值大于90的影響自動(dòng)控制系統(tǒng)故障時(shí)間的81%的輸入因子,然后對(duì)該23個(gè)重要的輸入因子再進(jìn)行FMEA(失效模式分析),進(jìn)一步找出最關(guān)鍵的輸入因子。
三、A階段
A階段的目的是確定關(guān)鍵因子確實(shí)是這些嗎。本項(xiàng)目通過前一階段的快速改善,系統(tǒng)故障明顯降低,但距離目標(biāo)值還有一定差距。結(jié)合沒有明顯改善的兩個(gè)因子程序設(shè)計(jì)的合理度和磨內(nèi)壓差設(shè)定進(jìn)行分析改進(jìn)。由于程序不合理明顯對(duì)總的故障時(shí)間有影響,本項(xiàng)目不再進(jìn)行A階段分析,直接進(jìn)行程序優(yōu)化,降低故障時(shí)間。
通過前階段快速改進(jìn)時(shí)發(fā)現(xiàn),輥壓設(shè)定和風(fēng)量設(shè)定兩個(gè)參數(shù)對(duì)磨機(jī)的故障有影響,通過參數(shù)的調(diào)整,提高磨機(jī)的運(yùn)行穩(wěn)定性,降低故障時(shí)間。基于以上原因,對(duì)兩個(gè)因子進(jìn)行合并考慮,其他系統(tǒng)參數(shù)暫不進(jìn)行完善改進(jìn)。
四、I階段
I階段是DMAIC過程獲得具體解決問題方案的關(guān)鍵階段,使用假設(shè)檢驗(yàn)對(duì)程序優(yōu)化前、后進(jìn)行比較,并對(duì)影響故障時(shí)間長(zhǎng)的關(guān)鍵因子磨內(nèi)壓差進(jìn)行DOE試驗(yàn)分析,建立RSM擬合模型與優(yōu)化設(shè)計(jì)。
1、使用假設(shè)檢驗(yàn)對(duì)程序優(yōu)化前后進(jìn)行比較
首先建立假設(shè):改進(jìn)后故障時(shí)間的平均值是否顯著降低?通過改進(jìn)前、后故障時(shí)間的平均值的單值圖和箱線圖粗略地可以看出有所降低,為了準(zhǔn)確,繼續(xù)研究P值。經(jīng)雙樣本T檢驗(yàn)后,P值=0.000<0.05,故障時(shí)間的平均值確實(shí)有所降低,因此改進(jìn)有效。
2、全因子試驗(yàn)設(shè)計(jì)
通過A階段得出磨機(jī)的穩(wěn)定性對(duì)超細(xì)粉自動(dòng)控制系統(tǒng)運(yùn)行影響顯著;而通過I階段分析可知輥壓設(shè)定和風(fēng)量設(shè)定兩個(gè)參數(shù)對(duì)磨機(jī)的穩(wěn)定性影響比較大。我們要判斷哪個(gè)因子的主效應(yīng)顯著?哪個(gè)因子的交互效應(yīng)顯著?什么條件下可以獲得最佳的運(yùn)行穩(wěn)定性?則需要通過DOE試驗(yàn)來得出結(jié)論(每個(gè)參數(shù)試驗(yàn)時(shí)間為1d)。
輥壓:低水平為94 bar,高水平為98 bar。
風(fēng)量:低水平為845 r/min,高水平為855 r/min。
準(zhǔn)備做全因子試驗(yàn)重復(fù)4次,中心點(diǎn)4次試驗(yàn)。
①參數(shù)試驗(yàn)設(shè)計(jì)分析
從方差分析表中可以看出,輥壓和風(fēng)量的P值=0.000<0.05,說明輥壓和風(fēng)量對(duì)磨內(nèi)壓差影響顯著,相互間的二階交互P值全部為0.000,說明相互間的二階交互作用對(duì)磨內(nèi)壓差影響顯著。主效應(yīng)項(xiàng)P值=0.000<0.05,說明模型有效。彎曲項(xiàng)p值=0.824>0.05,說明模型無彎曲。
②參數(shù)試驗(yàn)設(shè)計(jì)殘差分析
觀察以觀測(cè)值順序?yàn)闄M軸的散點(diǎn)圖,殘差無不正常的升降趨勢(shì);觀察響應(yīng)變量擬合值的散點(diǎn)圖,殘差無“漏斗型”或“喇叭型”,此圖正常;殘差服從正態(tài)分布。由殘差分析,可以判斷實(shí)驗(yàn)?zāi)P秃线m。
③參數(shù)試驗(yàn)設(shè)計(jì)分析(回歸方程式)
磨內(nèi)壓差的系數(shù)估計(jì),使用未編碼單位的數(shù)據(jù)。
回歸方程式為:磨內(nèi)壓差=1440.2-15.2906輥壓-1.70375風(fēng)量+0.018125輥壓x風(fēng)量。
④主效應(yīng)和交互效應(yīng)分析
從輥壓、風(fēng)量的主效應(yīng)圖可以看出,輥壓、風(fēng)量均與磨內(nèi)壓差成正比關(guān)系,從交互效應(yīng)圖可以看出,兩條線不平行,說明輥壓和風(fēng)量存在交互作用。
⑤等值線圖、響應(yīng)曲面圖(見圖3)

圖3
從磨內(nèi)壓差與輥壓、風(fēng)量的等值線圖上看出,輥壓在94-98 bar之間取值,風(fēng)速在845-855 r/min之間取值,磨內(nèi)壓差能達(dá)到理想要求。
從磨內(nèi)壓差與輥壓、風(fēng)量的曲面圖上看出,曲面有扭曲現(xiàn)象,說明風(fēng)量與輥壓存在交互作用。
⑥實(shí)現(xiàn)最優(yōu)化
通過調(diào)優(yōu),當(dāng)輥壓為94 bar,風(fēng)速為845 r/min時(shí),磨內(nèi)壓差能達(dá)到理想要求。
五、C階段
C階段的主要工作是對(duì)改進(jìn)成果進(jìn)行固化納標(biāo),并對(duì)Y的SPC監(jiān)控。
①改進(jìn)后故障時(shí)間工程能力計(jì)算
改進(jìn)后,超細(xì)粉自動(dòng)控制系統(tǒng)故障時(shí)間的能力指數(shù)Cpk=1.27(改進(jìn)前0.64),西格瑪水平Z=3.81(改進(jìn)前1.92),能力指數(shù)比改善前有所提高。
②實(shí)施對(duì)Y的SPC監(jiān)控
從超細(xì)粉自動(dòng)控制系統(tǒng)故障時(shí)間的SPC圖來看,故障時(shí)間是穩(wěn)定受控的。
③對(duì)改進(jìn)成果進(jìn)行固化納標(biāo)
在控制階段,對(duì)M、I各階段實(shí)施的改進(jìn)措施進(jìn)行文件化、制度化,從而加強(qiáng)控制。
④項(xiàng)目改進(jìn)成果
超細(xì)粉自動(dòng)控制系統(tǒng)故障時(shí)間由改善前的467 min/月降低到改善后的261.5 min/月,自動(dòng)控制系統(tǒng)穩(wěn)定性得到有效控制。
實(shí)施改進(jìn)措施后進(jìn)行故障時(shí)間跟蹤記錄,至活動(dòng)結(jié)束時(shí)故障時(shí)間呈逐月下降趨勢(shì),表明采取的措施是有效的。
六、結(jié)語
在降低超細(xì)粉自動(dòng)控制系統(tǒng)故障時(shí)間的項(xiàng)目實(shí)踐過程中,天行健咨詢專家依據(jù)六西格瑪管理的方法論,關(guān)注每個(gè)工序和指標(biāo)參數(shù)對(duì)故障時(shí)間的影響,聚焦到多個(gè)問題點(diǎn),進(jìn)而系統(tǒng)性的分析問題、分解項(xiàng)目,針對(duì)不同的問題,使用了六西格瑪?shù)亩喾N工具綜合加以解決,而且每個(gè)工具和分析方法的使用都可以根據(jù)實(shí)際問題靈活運(yùn)用,最終取得了良好的效果,為維護(hù)行業(yè)精細(xì)化水平的提高提供了新思路。