六西格瑪管理是領導承諾的全面質量管理,為了有效地推進六西格瑪管理,某鋼鐵集團管理層聘請天行健管理公司專家顧問進行封閉式培訓;專業部門領導帶隊到國內的組織去參觀學習。2011年計劃并完成106個項目,并將“六西格瑪管理”納入組織文化及公司方針目標。冶金行業、機械加工制造業等也在推行六西格瑪管理。這些說明了“六西格瑪管理”已逐步被我國鋼鐵冶金組織認同。在認真學習“六西格瑪管理”理論,了解國內外成功運用該方法經驗的基礎上,該鋼鐵集團確定三煉鋼廠、熱軋廠、大型廠和軋板廠作為試點單位。
1、培訓目標:完成一個六西格瑪黑帶項目,按項目計劃給組織創造50萬元以上的財務收益。
2、項目都緊密結合公司發展方向,如熱軋廠圍繞硅鋼、HiB鋼、降廢減損;三煉鋼廠圍繞降廢、降低消耗、提高產能等;大型廠圍繞提高高線產品質量;軋板廠圍繞提高常化一次性能合格率等等。
3、以降低工藝因素的中間軋廢作為提高正品率和成材率,快速向用戶交付產品,提高用戶滿意度,攻關目標值為:正品率由<93%提高到>96%(合格率提升到>99.45%的水平)。
一、進行分層次分系統的培訓
2011年3月,該集團聘請天行健管理公司專家對公司級領導和二級單位高、中層領導進行了為期一周的六西格瑪管理知識培訓。4月份,又在公司舉辦的六西格瑪管理高級研討班授課,對公司選拔的六西格瑪管理骨干30多人進行了封閉式培訓,為項目正式啟動提供了人力資源方面的保證。
二、六西格瑪項目的選定與推進
該公司六西格瑪管理的“DMAIC”模式,即以項目為載體,每個項目分“D-定義、M-測量、A-分析、I-改進、C-控制”五個階段推進的模式。導入方式為:項目培訓與項目實施結合進行,因此六西格瑪培訓過程實際上也是項目實施過程。DMAIC五個階段,每個階段第一周集中培訓。其余三周學員在崗位進行項目實踐,兩次培訓間進行一次輔導,持續4~6個月,每個黑帶不間斷地邊學邊做,每一階段都對項目進展情況進行檢查回顧。培訓目標:完成一個六西格瑪黑帶項目,按項目計劃給組織創造50萬元以上的財務收益。
2011年5月份,專家顧問對三煉鋼廠、熱軋廠、大型廠和軋板廠的領導和技術人員進行了篩選項目的專門培訓。對選定六西格瑪項目的原則方法、流程步驟,以及篩選標準和工具進行講解。確定了14個“六西格瑪管理”項目(三煉鋼9個、一熱軋3個、大型廠1個、軋板廠1個)。所選項目都緊密結合公司發展方向,如熱軋廠圍繞硅鋼、HiB鋼、降廢減損;三煉鋼廠圍繞降廢、降低消耗、提高產能等;大型廠圍繞提高高線產品質量;軋板廠圍繞提高常化一次性能合格率等等。
三、鋼鐵公司大型廠實施六西格瑪管理做法
大型廠高速線材生產線是重點工程。高線在過去7年的生產中已取得了較好的成績:質量方面,SWRM8、H08、WDT47A等多個“雙高”品種獲得品實物質量金杯獎;產量方面,年產量從40萬噸穩步上升到70萬噸;市場方面,以SWRH82B(制預應力鋼鉸線用)、72A-L(制鋼簾線用)為代表的50多個“雙高”新品種已實現批量生產,市場前景良好。但是,自2008年以來,高線效益品種鋼的訂貨量增長緩慢,用戶對產品質量異議量有所增加。因此,大型廠決定把提高高線產品質量作為試點的項目。按六西格瑪管理的五步循環改進法:定義(Define)、評估(Measure)、分析(Analyze)、改進(Improve)、控制(Control)方法,或稱為DMAIC方法,本次改進工作開展如下:
1、定義顧客需求(Define)
確定目標為:以降低中間軋廢提高正品率和成材率,快速向用戶交付產品,提高用戶滿意度,攻關目標值為:正品率由<93%提高到>96%(合格率提升到>99.45%的水平)。
2、評估當前績效(Measure)
大型廠搜集了2010年高線軋鋼廢鋼支數,并針對工藝廢鋼和設備廢鋼進行了分類統計如下表:
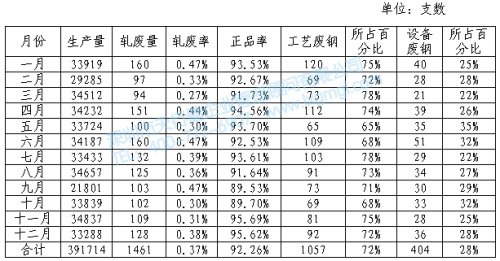
對現狀評估如下:
由上表中的數據得知,高線一級品率的σ績效值為3.21σ,屬于中間層次的σ績效值,亦說明在高線提高成材率上我們有許多的工作可以做,用戶的滿意度可以進一步的提高。從上表統計數據我們可以看出,設備因素所造成的廢鋼是次要的占34%,而主要的是工藝因素廢鋼占72%。為此,大型廠應用六西格瑪管理確定:以降低工藝因素的中間軋廢作為提高一級品率和成材率的優先次序予以解決,攻關目標值為:正品率由<93%提高到>96%(合格率提升到>99.45%的水平)。
3、原因分析(Analyze)
①由于人員的經常變動,操作水平的參差不齊,加上工作態度不認真,責任心不強,是造成堆鋼的根本原因。
②操作人員導衛安裝方法不當,造成導衛磨損嚴重或搭鐵,而又不能及時發現處理,是造成堆鋼的又一大問題。
③操作人員在設置輥縫時不正確。后果是:輥縫大,軋件尺寸大,進口導衛損壞,堆鋼;輥縫小,軋件尺寸偏小,下一機架進口導衛不能有效夾持倒坯堆鋼。
④軋件變形量增大,變形阻抗力隨之增大,造成輥環局部溫度快速增高而爆裂堆鋼。
⑤由于輥環的安裝不正確,錯輥,或者在軋制過程中卸壓,也是導致堆鋼的原因;冷卻水中的夾雜,堵塞冷卻水管,致使冷卻強度降低導致輥環爆裂而堆鋼。
⑥另外在設備上也有可能出現問題。比如:立式活套機構故障,側活套進入口導輪的調整,油氣潤滑以及活套掃描儀(HMD)不正常也會導致堆鋼。
4、改進措施(Improve)
①實行競爭上崗制度,對崗位實施兼并和優化組合,組成工作上的互補。
②嚴格實行經濟責任制考核,落實分解責任到崗位到個人。
③推行和全面實施標準化作業,制定和完善工藝調整辦法,納入B標準管理。
④在全線崗位推行生產過程控制,落實公司工序控制點的檢查,加強軋線各機架間變形量的控制,防止軋件變形阻力過大而堆鋼。
⑤推行全面設備點檢制度落實,正確安裝輥環、導衛及冷卻水管,并在停機時著重檢查。
⑥長期性培訓計劃,鍛煉大工種作業能力,配合機電氣人員對立式活套等設備進行檢查,確保其工作狀態完好。
對策實施進程表
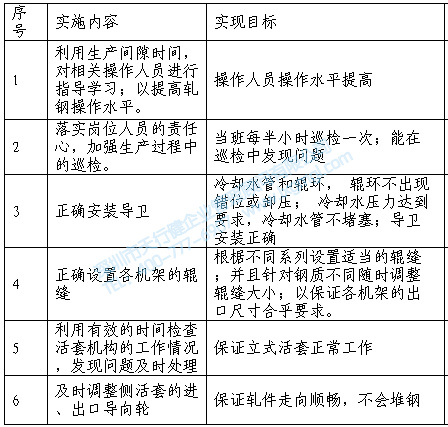
5、控制實施(Control)
①成立以車間主任為組長的培訓小組,制訂詳實的培訓計劃,提高軋鋼人員的技術水平。
②車間技術人員加大對生產崗位的工藝紀律檢查力度,保證生產過程的有效控制。
③落實上線的備品件的裝配到位,導衛、水管、輥環質量符合軋線要求,完善統計臺帳。
④輥縫設置納入綜合管理,生產數據記錄可查。
⑤加強控制和抽檢,保證活套工作正常。
⑥實施全線生產過程控制,保證軋件走向順暢。
2011年我們制定對策并嚴格按照實施后,取得了明顯效果。下圖是我們對2011年6月至12月廢鋼情況的統計。
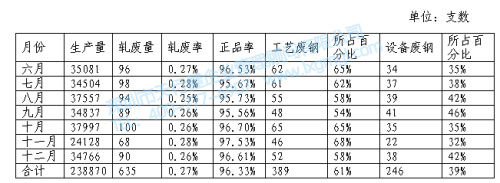
通過抽樣,現狀評估表:

①由于6σ的成功應用實施,高線正品率由92.26%升到96.33%(合格率提升到>99.45%的水平),工藝廢鋼比率由72%下降到61%,績效明顯。
②提高了高線設備的作業率和產品的成材率的質量指標的進一步提高,產能優勢得以進一步提高。
③質量指標的提升為我們的合同兌現和及時迅速交貨提供了保障,給用戶的滿意度增加。
④軋制廢品的減少,使高線的生產成本降低,產品的市場競爭力加強,拓展了高線的市場占有率。
⑤以顧客為中心的策略和持續的6σ管理法的應用改進,市場反應良好,顧客回頭率提高,高線的訂貨量持續增長。
經濟效率計算:
創造效益=直接效益+間接效益
直接效益=年產量(噸)×正品提高率×正材與廢鋼差價(元)
=700000×(96.33%-92.26%)×600
=1709.40萬元
間接效益=廢鋼處理時間(按考核指標5小時/月*12月/年=60小時)×小時產量(噸/小時)×噸鋼效益(元/噸)
間接效益=60×120×600=432萬元
創造效益=1709.40+432=2141.4萬元